Importance of aluminum welding
When it comes to welding, aluminum is a popular material choice for many people due to its lightweight and corrosion-resistant properties. Whether you’re working on automotive parts, aircraft components, or even household items, having the ability to weld aluminum can be a valuable skill.
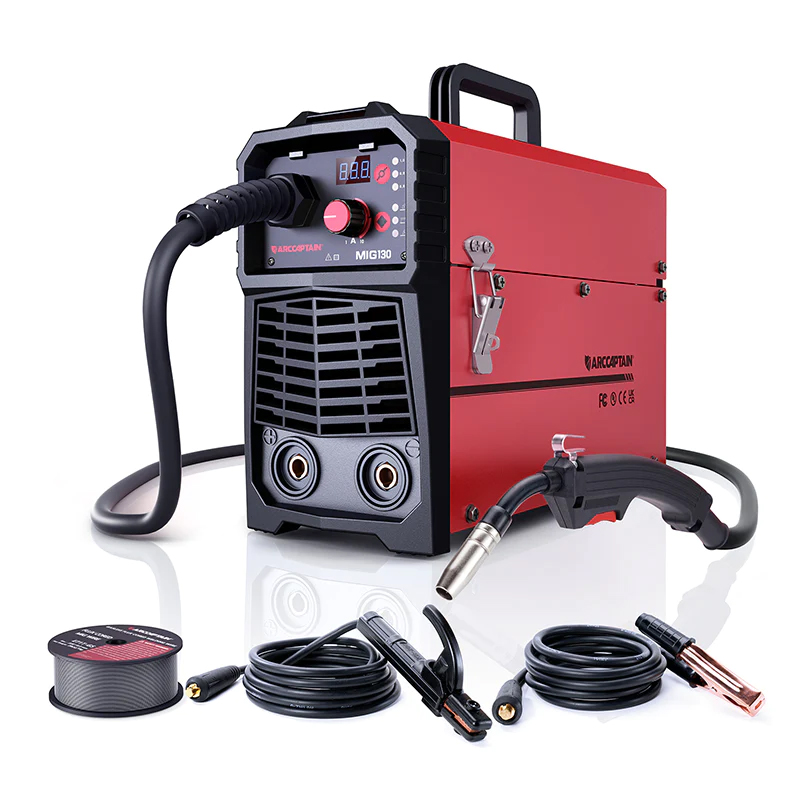
Aluminum welding requires the use of specialized equipment and techniques, and having the right welder can make all the difference. With the right welder, you can produce strong and clean welds on aluminum, ensuring that your projects are completed with precision and durability.
Investing in a quality aluminum welder can also expand your capabilities and open up new opportunities for your welding business. You’ll be able to take on a wider range of projects and work with a variety of materials, making your services more valuable to potential clients.
Overall, aluminum welding is an important skill to have in the welding industry, and having the right welder can make it easier and more efficient. So, if you’re looking to take your welding skills to the next level and expand your capabilities, consider investing in a reliable aluminum welder. It will not only enhance your work but also the quality of the projects you complete.
Challenges in Welding Aluminum
Welding aluminum can be a bit trickier than welding other metals. The main challenge is that aluminum has a lower melting point, which means it can be more prone to warping and distortion during the welding process. Additionally, aluminum oxide forms quickly on the surface of the metal, which can make it more difficult to achieve a clean, strong weld.
To overcome these challenges, you need a high-quality welder that is specifically designed for aluminum welding. Our welders are built with the latest technology to ensure smooth, consistent welds on aluminum and other metals. With features like adjustable heat settings and precise control, our welders make it easier to tackle the challenges of welding aluminum.
Investing in a reliable welder is essential for anyone working with aluminum. Our welders are built to last and are a valuable tool for anyone looking to produce strong, high-quality welds on aluminum and other metals. Don’t let the challenges of welding aluminum hold you back – equip yourself with a top-of-the-line welder and tackle any aluminum welding project with confidence.
High thermal conductivity of aluminum
When it comes to selecting a welder for your projects, it’s important to consider the materials you’ll be working with. Aluminum is a popular choice for many applications due to its high thermal conductivity. This means that it can quickly and efficiently transfer heat, making it an ideal material for welding.
When using a welder with the ability to handle aluminum, you’ll find that it can produce high-quality welds with minimal distortion, reducing the need for extensive post-welding work. This can save you time and money in the long run. Additionally, the high thermal conductivity of aluminum allows for faster welding speeds, increasing productivity and throughput.
Investing in a welder that can handle aluminum with ease is a smart choice for anyone working with this material. It will allow you to produce strong, reliable welds while also improving efficiency and reducing the potential for error. Consider the benefits of high thermal conductivity when selecting a welder for your next project.
Formation of oxide layer on aluminum surface
Are you tired of dealing with the formation of oxide layers on aluminum surfaces during the welding process? It can be a frustrating and time-consuming issue that affects the quality of your welds. No one wants to spend extra time cleaning and preparing aluminum surfaces before welding. That’s why investing in a high-quality welder specifically designed for aluminum welding is so important.
Our TIG welders are engineered to tackle the challenges of welding aluminum, including the formation of oxide layers. With the right equipment, you can achieve clean and precise welds without the hassle of oxide layer interference. Our welders provide the power and precision needed to effectively weld aluminum, giving you the confidence to produce high-quality work every time.
Don’t let oxide layers on aluminum surfaces slow you down or compromise the quality of your welds. Upgrade to a welder designed for aluminum welding and experience the difference for yourself. Invest in a welder that can handle the challenges of welding aluminum and make your work easier and more efficient. With the right equipment, you can achieve professional results without the frustration of oxide layer formation. Choose a welder that is up to the task and take your aluminum welding to the next level.
Differences in melting points between aluminum and filler metal
When it comes to welding aluminum, it’s important to consider the differences in melting points between aluminum and filler metal. Aluminum has a lower melting point than many other metals, which means it can be a bit trickier to weld.
By using a high-quality welder specifically designed for aluminum welding, you can ensure that the filler metal melts at the right temperature to create a strong, durable bond. This is essential for ensuring the integrity of your welds and preventing any potential weaknesses in the finished product.
The right welder can provide the precise heat control needed to match the melting points of both the aluminum and the filler metal, resulting in a smooth, efficient welding process. Plus, with the right equipment, you can achieve clean, professional-looking welds without any hassle.
Investing in a welder that can handle the differences in melting points between aluminum and filler metal is a smart choice for people who regularly work with aluminum. It can make your welding jobs go much smoother, and the finished products will be of the highest quality.
Factors Affecting Aluminum Welding
Are you in the market for a new welding machine? Whether you’re a professional welder or a hobbyist, it’s important to consider the factors affecting aluminum welding when choosing a new machine. Aluminum welding requires a specific set of skills and equipment, and not all welders are created equal when it comes to welding this material.
One important factor to consider is the power source of the welder. For aluminum welding, a machine that can provide consistent and stable power is essential. Look for a machine with a high-frequency start and a stable arc to ensure clean and precise welds.
Another factor to consider is the type of welding process the machine is capable of. While there are a variety of welding processes, not all are suitable for aluminum welding. Look for a machine that is capable of both TIG and MIG welding, as these processes are best suited for welding aluminum.
It’s also important to consider the overall build quality and durability of the machine. Aluminum welding can be more challenging than welding other materials, so you’ll want a machine that can withstand the demands of the job. Look for a machine with a sturdy construction and high-quality components to ensure longevity and reliable performance.
Lastly, consider the ease of use and user-friendly features of the machine. Look for a welder with intuitive controls, adjustable settings, and a clear display for easy operation. Additionally, consider the portability and size of the machine, especially if you need to transport it to different job sites.
When considering all of these factors, it becomes clear that not all welders are suitable for aluminum welding. Take the time to research and compare different options to find the best welder for your aluminum welding needs. Investing in a quality welder that meets the specific requirements of aluminum welding will ultimately save you time, money, and frustration in the long run.
Choice of welding process
When it comes to choosing a welding process, it’s important to consider the type of work you’ll be doing and the materials you’ll be working with. Different welding processes have different strengths and weaknesses, so it’s important to choose the one that best fits your needs.
For example, if you’ll be working with thin materials or in tight spaces, you may want to consider a TIG (tungsten inert gas) welding process. TIG welding is known for its precision and ability to work with a variety of materials, making it a good choice for a wide range of applications.
On the other hand, if you’ll be working with thicker materials or need to lay down a lot of weld quickly, you may want to consider a MIG (metal inert gas) welding process. MIG welding is known for its speed and ease of use, making it a popular choice for production work and larger projects.
Ultimately, the choice of welding process will depend on your specific needs and the type of work you’ll be doing. It’s important to do your research and consult with knowledgeable people to ensure you choose the right welding process for your needs. With the right welding process, you can tackle your projects with confidence and precision.